
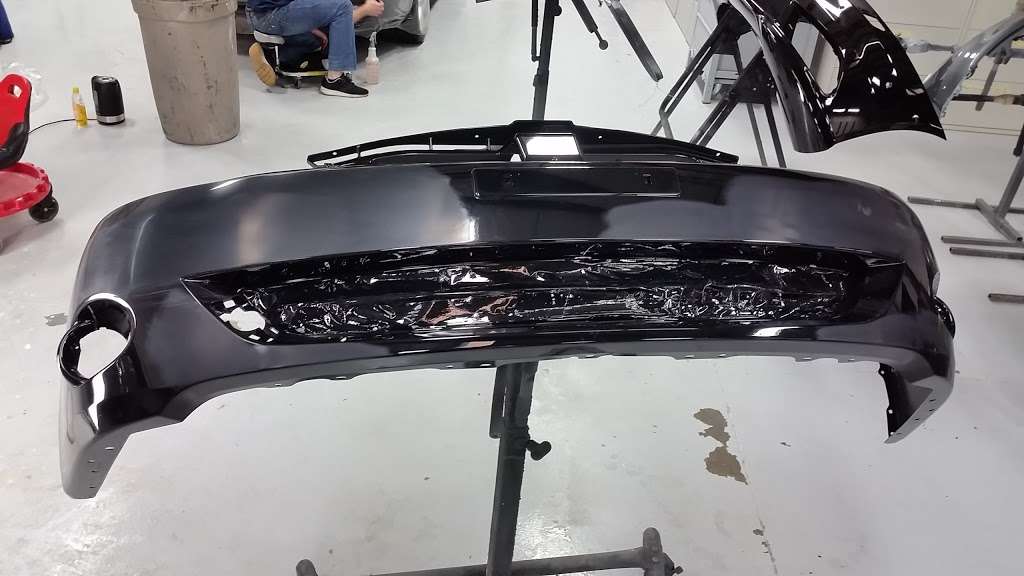
While I’ve talked about 3d printing in a previous post, I should point out I now own 6 different 3d printers, each one getting bigger, and more complex. Needless to say, she won first place in the “best design” category. In this video, one of my daughter’s had designed her pinewood derby car on the computer, and we let the CNC machine do all of the work. The x-15 build lower on the page c ould not have been built without a CNC machine. What is really exciting about a CNC machine is it can go well beyond the basic building blocks, to build extremely complex parts. Makes things like fins, AV bays and centering rings trivial to make to exact specifications. I sure do love tools controlled by computers! In this case, I can build on my computer exactly what I want cut out in 3 dimensional space, then the CNC machine will do all the work to very, very tight tolerances. Le bolted to a computer controlled gantry. The secret sauce is in the software, which can control the number of wraps, and the angle of each wind to create very specific circumferential, or longitudinal tensile strength. The entire machine is built with 8020 extruded aluminum, and the same stepper motors I use in 3d printing. The first one didn’t go so well, but the second was successful. An enterprising guy named Turner Hunt decided to try and make a hobby version, and launched a kickstarter. These highly specialized machines normally cost 50,000 to 100,000 dollars.

This is a computer controlled machine which which allows me to make the rocket sustainers, and other parts out of any kind of filament. I’ve also spent a week rebuilding the electronics in a McDonalds happy meal that stopped working, and brought my eldest daughter to tears…… At one point in my life, I was lucky enough to own an Apple 1, and successfully brought it back to life. One of my old hobbies was collecting vintage computers, which provided me hours and hours of electronics board repair training.
#Ultimate paint shop lake bluff professional#
In fact, my reflow and rework station equipment is professional grade including IR camera’s and a robotic arm to help my sausage fingers manage the tiny SMT bits and pieces being made today.
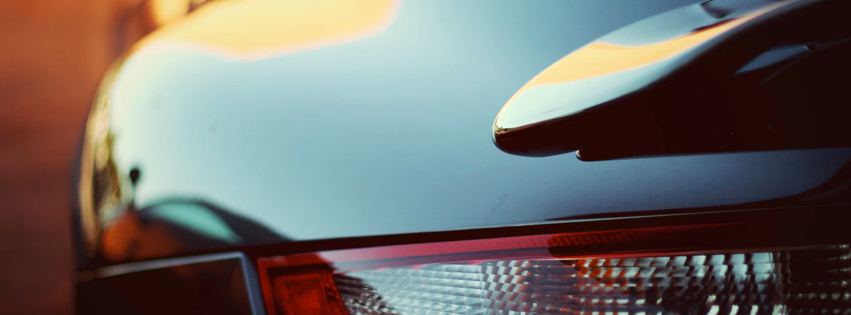
In this case, I often stumble in the original build, but I’ve gotten really good at reworking a board. I’m like the baseball player that can’t hit the ball, but sure can run the bases. With the number of soldering guns and stations I own, you would think I’d be good at it by now, but I’m not. While the boards themselves are milled on my cnc machine (which you’ll see in a bit), most of the fun is in my basement office, which happens to also be a good soldering bench. I build a lot of electronics for fun, including custom electronics for rocketry. The fun begins with equipment not often found in your typical shop. This is an alternate view of my 99 mm aluminum tig-welded fincan that fits perfectly over a 98 mm motor case, which I will be using as the booster section of a minimum diameter sounding rocket I am working on. There are some areas in rocketry in which there is no better alternative then metal, in my case, aluminum. I guess the one tool in this area that is not found in your average garage is a TIG welder. Nothing really special here, and I’ve tended to go cheap (think Harbor Freight) on many items because I just don’t use them often enough to appreciate the difference. Drill press, table saw, giant mixers, scroll saws, bench sanders, and lots of tools. So, this will be a short tour through my workshop.įirst, what I’m not going to show you – the “base” of my workshop looks a lot like someone poured a mechanic’s garage into a woodworkers toolshed, and threw in some culinary equipment. I’ve recommended my own blog of course, but realized the level 3 build which started this blog didn’t discuss any tools, or core manufacturing techniques at all. The most common question I get from people who first find out I enjoy rocketry (after – “is it legal?”) is how the rockets are built, and what kind of tools do I use.
